Workplace Environment Testing is the Responsibility of Every Employer with a Workspace
For each type of work, there are prescribed values that the workplace must meet. Testing of workplace environmental factors must be conducted to determine whether the measured values are within the limits specified by regulations and standards. Testing in the workplace environment can only be carried out by authorized personnel.
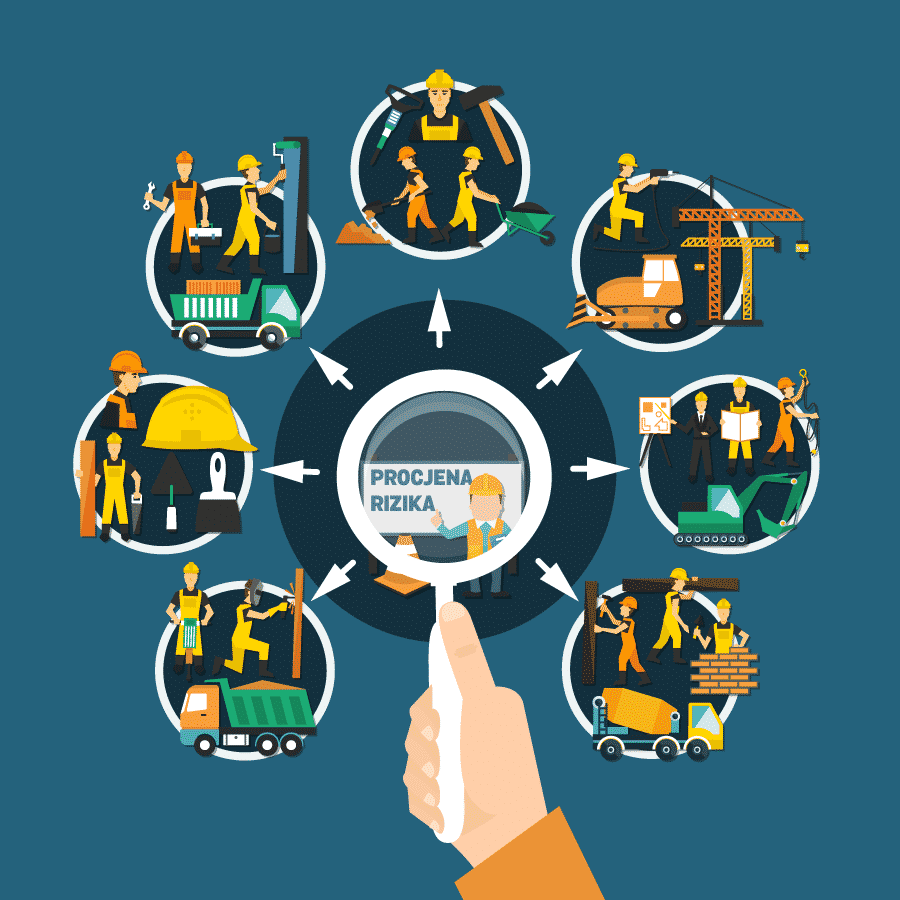
Testing of the Working Environment
Testing of the working environment is one of the measures defined during the creation of a risk assessment at work.
At least once every three years, it is necessary to conduct testing of working environment factors (illumination, noise, microclimate, chemical hazards) to determine whether the measured values are within the limits specified by regulations and standards and to react if they are not.
To assess compliance with health requirements in the workplace environment, prescribed (permissible) values of exposure to hazards in the workplace, as determined by occupational safety regulations or corresponding Croatian standards, are used. A report is prepared after conducting the testing of the working environment. The testing itself does not require work stoppage - on the contrary! The point of testing is to conduct measurements in real working conditions.
In the workplace, employees are exposed to various hazards that can cause injuries or harm to their health and work ability. Undesirable consequences occur when there are disruptions in the relationship between a person and their environment. Adverse factors in employees can lead to fatigue, dissatisfaction at work, reduced concentration and work ability, injuries, and occupational diseases.
Workspaces and the working environment are regulated, and care must be taken when designing work facilities. Buildings and rooms intended for work, as well as auxiliary rooms, must be constructed in accordance with occupational safety rules. Room dimensions, walls, floors, doors, windows, pathways, heating, ventilation, and all installations must match the room's purpose to provide employees working in these spaces with suitable working conditions.
To determine whether the working environment complies with conditions specified by occupational safety rules, testing must be conducted in workspaces (and outside workspaces) where:
- The work process affects temperature, humidity, and air flow rate.
- Dust is generated during the work process.
- Noise or vibrations are generated during the work process.
- Hazardous chemicals are used, produced, or processed during work.
- There is exposure to hazardous radiation during work.
- There are risks of explosive atmospheres during work.
- Appropriate lighting is required based on risk assessment.
Testing of Work Equipment
Hazards arising from the use of machinery and equipment for work are categorized into three groups:
- Mechanical sources of hazards
- Hazards from power sources and drive systems
- Hazards in the working environment
Specific types of machinery and equipment with increased hazards are referred to as machinery and equipment with increased hazards. Machinery and equipment with increased hazards include, in particular: cranes with a lifting capacity exceeding 10 kN, cargo lifts, industrial conveyors, mechanized internal transport vehicles, machines for processing and processing wood, metal, and similar materials, mechanical and hydraulic presses, lifting platforms, compressors, centrifuges, pre-pressure and vacuum chambers, central heating boilers, steam and hot water boilers, machines and equipment containing pressure vessels, and other machinery and equipment with similar hazards to the safety and health of employees.
Unless otherwise regulated by special regulations, machinery and equipment with increased hazards must be tested:
- Before they are put into use.
- At least once every two years of use.
- After reconstruction and before resuming use.
- Before use at a new location if the machinery and equipment have been moved from one location to another and have been disassembled and reassembled as a result.
Testing of Fire Hydrant Systems
The hydrant system must have a secure water supply, unless otherwise specified by special regulations. The internal fire hydrant system must have a secure water source with a capacity that allows the supply of at least the minimum required flow rate of water needed to protect the fire sector with the highest specific fire load in the building being protected, with a nozzle pressure not less than the pressure specified by these regulations, for a minimum duration of 60 minutes. The external fire hydrant system must have a secure water source with a capacity that allows the supply of at least the minimum required flow rate of water needed to protect the fire sector with the highest fire load in the building being protected, with a pressure at the hydrant not less than the pressure specified by these regulations, for a minimum duration of 120 minutes.
If a building that uses both an external fire hydrant system and an internal fire hydrant system as a secure water source uses special water tanks, their volume must be at least equal to the sum of the total water quantity for each individual hydrant system. Certain types of hydrant systems do not need to operate simultaneously. The required amount of water for extinguishing with the hydrant system must be provided independently of other consumers supplied with water from the same source. If an exhaustible water tank is used as a secure water source as mentioned in paragraph 2 of this article, the volume of water must not be less than 1 m3. The capacity of the secure source must be proven by the pumping procedure in the most unfavorable meteorological conditions, except when a water supply network, non-exhaustible natural accumulation, or water tank
How often must the testing of the working environment be repeated?
This testing should be conducted every 3 years.
Does the testing of the working environment apply to the company or the space the company uses?
It applies to both. Each company must conduct this testing under its own name. Even in situations where multiple companies share the same space, each company must conduct the testing for itself.
What if we move to a new space?
In the case of relocation, the old testing no longer applies. Since you have changed locations, it is logical that testing must be conducted for the new space.
- Testing of physical factors (temperature, relative humidity, air velocity, illumination, noise, and vibration)
- Testing of chemical factors (concentration of gases, vapors, dust, and aerosols)
- Testing of biological factors.
- When the work process affects temperature, humidity, and air velocity
- When it is necessary to provide adequate illumination during work
- When noise or vibrations occur in the work process
- When gases, vapors, dust, or aerosols are generated during the work process
- When there is a possibility of exposure to biological hazards (agents) used in work outside primary physical isolation.
- Immediately after the conditions or changes that require testing have occurred
- Based on the decision of the labor inspector
- Periodically at intervals not exceeding three years, unless otherwise specified by special regulation.
Specialist for this service is:
Tomislav Nimac
Senior Expert in Occupational Safety