Training employees to work safely is the obligation of every employer who employs at least one person.
Every person in Croatia, in any workplace, must be trained to work safely. The training involves the employee, the employer, and the occupational safety expert. When conducting training, the employee's work processes and the work environment in which the employee performs the job are taken into consideration.
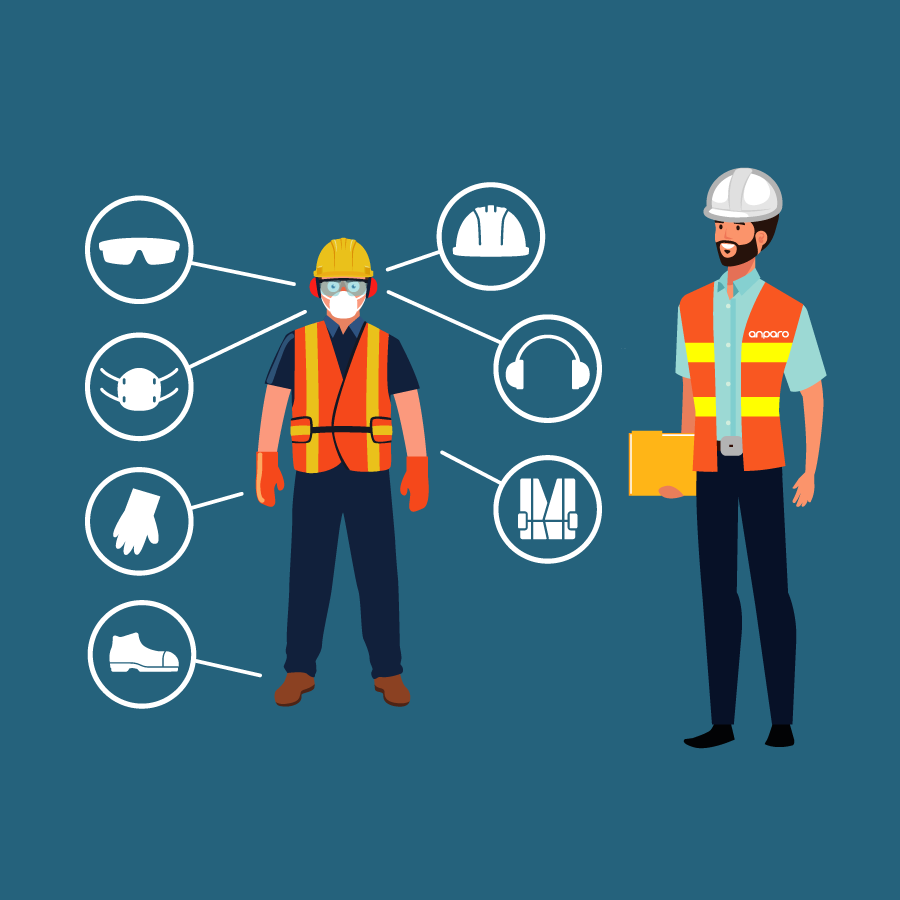
FOR EMPLOYERS WHO WANT TO LEARN MORE ABOUT TRAINING EMPLOYEES FOR SAFE WORK
Training employees for safe work is the obligation of the employer, regardless of the number of employees and the type of activity performed. This obligation arises from the Law on Occupational Safety. The employer is required to conduct employee training during working hours at their own expense. An untrained employee should not be allowed to work, except under the direct supervision of a trained employee for a maximum of 60 days from the date of employment. The training of employees for safe work, as well as the documents resulting from it, do not constitute an independent act. To carry out this training, the employer must have a risk assessment and an employee training plan.
At Anparo, we can conduct training in two ways. One is the traditional way of training employees for safe work in person: in this case, lectures are organized at the employer's premises, followed by an exam. The other method is online training through our online application for training employees for safe work. In this case, all employees will receive study materials and links to the exams in their email addresses. The advantage of this method of training employees for safe work is that employees can access the training at a time that suits them best.
What is the deadline for training a new employee?
The legislator has determined that a new employee must be trained for safe work within 2 months from the date of employment. Until then, they can work without it, but not independently, under the supervision of trained colleagues.
If an employee has already undergone this training in a previous job, is it still valid?
No, it is not. This training must be repeated for each new employer.
If an employee changes their job position or job description, do they need to be retrained?
Yes, they do. The ZOS form, which is issued as proof of training, must clearly highlight all work processes that the employee performs, and this information must always be kept up to date.
According to the Occupational Safety Act, the employer is obligated to provide training for employees to work safely, regardless of the number of employees and the nature of the work they perform. Training is conducted before starting work at a specific job position and in the case of changes in work procedures, the introduction of new equipment or technology, the reassignment of employees to new tasks or workstations, or when health damage is determined due to workplace hazards, harmful factors, or job-related stress.
The obligation of training also applies to individuals at work, except for scientists, apprentices, students in internships, and other individuals in the vocational education system who are not allowed to perform tasks independently and must work under the constant supervision of a qualified person, a teacher, or a mentor. Regardless, these individuals must still be informed about all facts and circumstances that affect or could affect safety and health, as well as about workplace hazards and potential risks they may be exposed to, in order to eliminate the slightest probability of work-related injuries.
What do we learn in Employee Training for Safe Work?
The specialist for this service is:
Tomislav Nimac
senior expert in occupational safety
What do we learn in Employee Training for Safe Work?
Workplace and Working Environment
In the workplace, employees are surrounded by various hazards that can cause injuries or harm to their health and work capacity. Undesirable consequences occur in the event of disruptions in the relationship between a person and their environment. Adverse factors in employees can lead to fatigue, job dissatisfaction, reduced concentration and work capacity, injuries, and occupational and other illnesses.
Workspaces and working environments are regulated, and they must be taken into account when designing work facilities. Construction facilities and rooms intended for work, as well as auxiliary rooms, must be constructed in accordance with occupational safety regulations. Room dimensions, walls, floors, doors, windows, walkways, heating, ventilation, and all installations must correspond to the purpose of the room to provide employees in workspaces with suitable working conditions.
In this section, we cover the following topics:
- Physical Factors
- Microclimatic Conditions
- Noise and Vibrations
- Radiation
- Chemical Hazards
- Gases and Vapors
- Dust, Smoke, and Mists
- Acids and Alkalis
- Biological Hazards
- Movement at Work
- Warning Signs in the Workplace
Working with Computers
A workstation with a computer should not be a source of danger for employee injuries or health damage. Employers are required to conduct a hazard assessment for all computer workstations, taking into account potential health risks to workers, especially due to visual, static, and psychological stress. Based on the hazard assessment, measures must be taken to eliminate identified deficiencies, taking into account the special and/or combined effects of identified hazards and harmful factors. The workstation equipment must not pose a risk of injury or health damage to employees.
In this section, we cover the following topics:
Machinery and Equipment for Work
Certain types of machinery and equipment for work are referred to as machinery and equipment for work with increased hazards. Machinery and equipment with increased hazards include, in particular: cranes with a capacity of over 10 kN, cargo lifts, industrial conveyors, mechanized internal transport vehicles, machines for processing and processing wood, metal, and similar materials, mechanical and hydraulic presses, lifting platforms, compressors, centrifuges, pre-pressurized and depressurized chambers, central heating boilers, steam and hot water boilers, machines and equipment containing pressure vessels, and other devices and machinery with similar safety and health hazards for employees.
In this section, we cover the following topics:
- Mechanical Sources of Hazards
- Hazard of stationary parts
- Hazards of rotating parts
- Clamping hazards
- Hazard of parts moving in a straight line
- Protective Devices
Hand Tools
Hand tools must be designed and maintained in such a way that, when used correctly, there is no risk of injury. Every individual should be familiar with the basic principles of safety when using hand tools and how to correctly apply tools in the work process. Hand tools are used in almost all areas of human activity, and this simplicity of use has led to the mistaken belief that no special knowledge and skills are required for the use of hand tools. The result of such an attitude is a large number of injuries when handling hand tools, most of which are minor (scratches or bruises), but there are also more serious consequences (infections, eye damage, and more severe injuries caused by sharp tools, etc.).
Electricity
The dangers of electricity are present all around us and are all the more significant because they are not visible, unlike some other sources of danger. Improper handling of electrical devices and inadequate safety measures are the main reasons for injuries when using electricity. In the case of untrained individuals, injuries usually occur because they cannot recognize potential danger, while for trained individuals, oversights and a casual attitude towards danger are the main reasons. Dangerous situations arise from employees' overconfidence, failure to follow rules, and lack of discipline at work.
Load Handling
Improper material handling can lead to very serious injuries. When materials are handled incorrectly, injuries to the spine, joints, heart and circulatory system, as well as mechanical injuries to the fingers, hands, feet, and legs, most often occur. Most accidents that occur when handling materials are the result of incorrect work habits, i.e., improper work methods, such as:
- Incorrect and unsafe gripping of objects
- Incorrect lifting, holding, and lowering of loads
- Lifting excessively heavy loads (overloading)
- Working without personal protective equipment.
In this section, we cover the following topics:
- Manual Transport
- Mechanized Transport
Personal Protective Equipment
Personal protective equipment (PPE) is any device or appliance that an individual wears or holds to protect against one or more hazards to health or life. PPE also includes any auxiliary or additional PPE that serves the same purpose.
Employees use PPE when working where it is not possible to eliminate risks to safety and health, and in cases where the employer cannot further reduce risks by applying basic OSH rules, technical measures, or appropriate work organization.
The use of PPE is the last safety measure to achieve safe working conditions, although the use of PPE can sometimes have advantages. PPE can be introduced into use almost immediately and can represent a temporary solution until other measures that require more time are implemented. PPE can also be a solution when the use of other measures is unacceptable, disproportionately expensive, or impractical in relation to the danger, the number of exposed employees, exposure time, and more.
Workers must use personal protective equipment exclusively for the purposes for which it is intended, maintain it in working condition, and protect it from damage.
In this section, we cover the following topics:
- Head Protection
- Eye and Face Protection
- Hearing Protection
- Respiratory Protection
- Hand Protection
- Body and Trunk Protection
- Foot Protection
First Aid
First aid procedures are performed by trained workers. After performing the prescribed first aid procedures, medical assistance must be provided to the injured or ill person.
In this section, we cover the following topics:
- Sudden Cessation of Breathing
- Sudden Cessation of Heart Activity
- Wounds
- Bone Injuries
- Eye Injuries
- Concussions
- Burns
- Chemical Burns
- Hypothermia and Frostbite
- Poisoning
- Heat Stroke and Sunstroke
- Electric Shock and Lightning Strike
- Ionizing Radiation
- Drowning
- Epileptic Seizure
- Unconsciousness
- Shock
- Choking
- Food Poisoning
- Bites from Poisonous Insects
- Bites from Poisonous Snakes
The specialist for this service is:
Tomislav Nimac
senior expert in occupational safety